We’re back with the second (and last) installment of “Jim, out of his depth.” In case you missed it, and care, here’s part 1: Sequential art (or, how I spent the week after Thanksgiving).
So, on with the picture show!
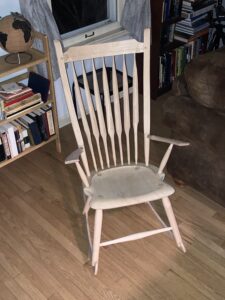
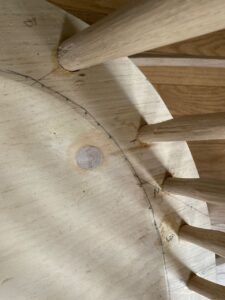
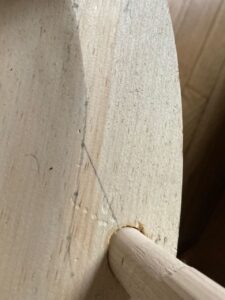
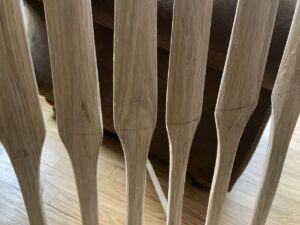
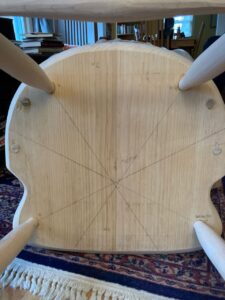
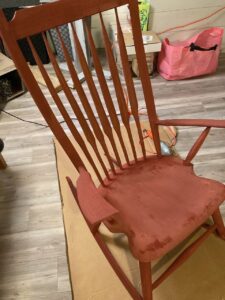
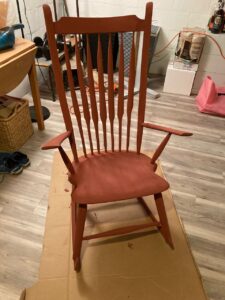
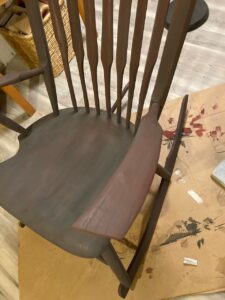
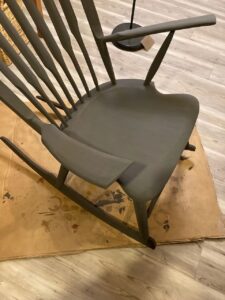
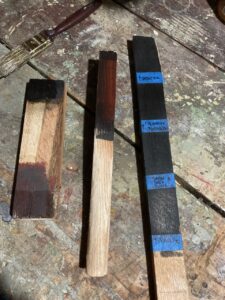
This led me to start with a couple coats of tung oil, thinned down with citrus-based solvent. That produced a very dull gloss, just barely more reflective than what you saw in the previous pictures. Also, I’d clearly not burnished enough since I was still picking up paint dust during the second go-round. Too late to fix that, but no worries! Following the advice of our instructor Luke, I planned to bring up the shine a bit in the final coat. My plan was to mix the tung+citrus with satin Osmo Polyx — a “blend of vegetable oils (sunflower, soybean and thistle) and waxes (carnauba and candelilla) combined with a small amount of low-odor solvent.” It’s sustainable and has minimal environmental impact.
Good plan, but while his recipe for a finishing coat had all the same basic ingredients and proportions (1/3 oil, 1/3 thinner, 1/3 poly), Luke at Sam Beauford suggested different types of each from what I used.
Now, I’m not a complete dope: I’d done some samples with various mixtures on some scrap oak, and it seemed to work, but between those sticks and the chair something went awry.
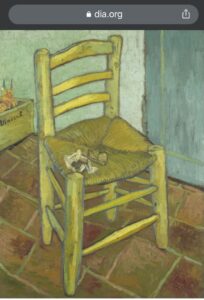
Fortunately, we planned to go to the Detroit Institute of the Arts to see the Van Gogh exhibit that day — and better still do so with some friends — so I had to leave the thing alone for a while. Couldn’t even look at it! I won’t pretend that at times that day I didn’t brood about ruining the damn chair, though, so I was no doubt occasionally bad, or at least distracted, company.
(The exhibit was great. Lunch was delicious. The friends are lovely.)
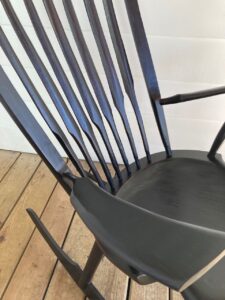
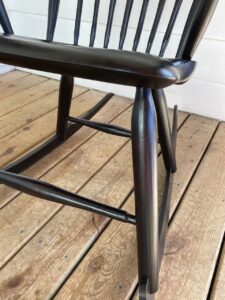
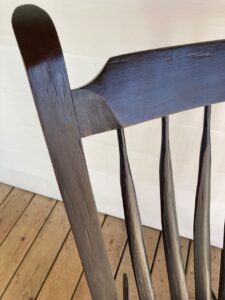
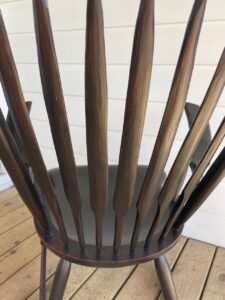
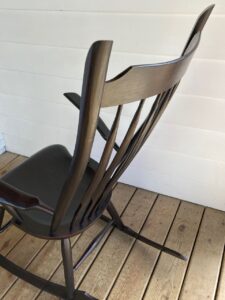
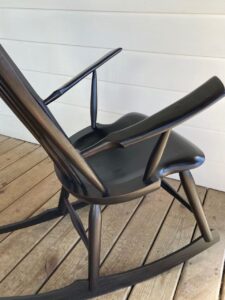
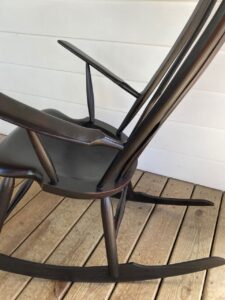
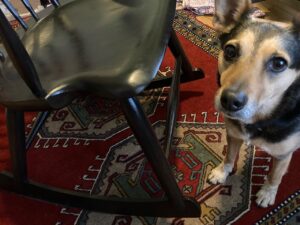
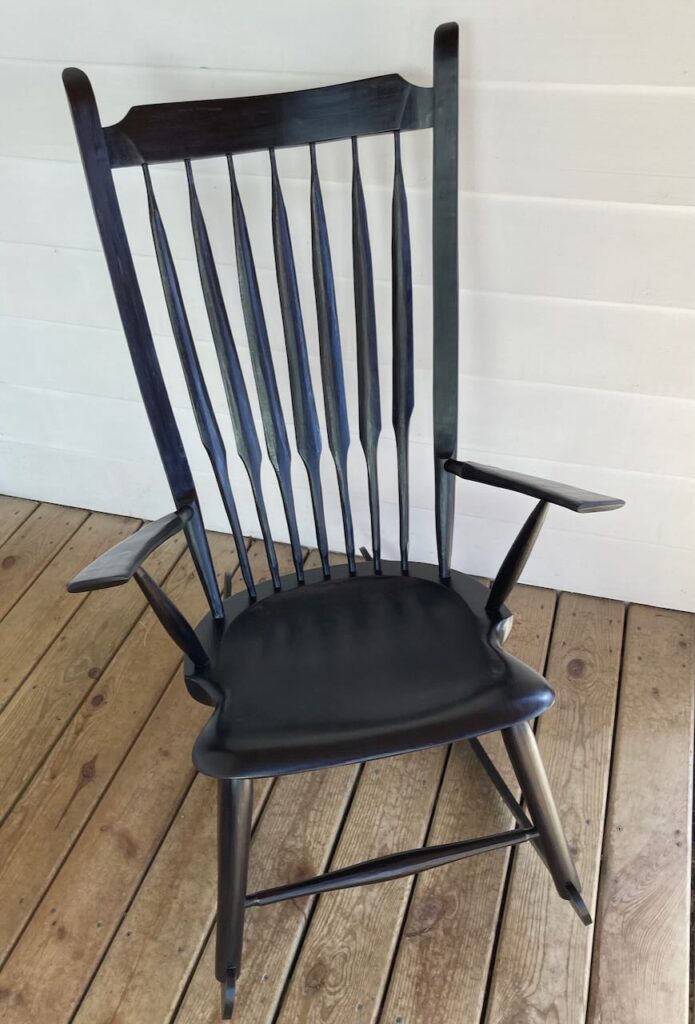